Redesign of a Cataract Surgery Tool
Cataract surgery is the most performed intervention in the world. It is performed using a process called phacoemulsification. This is done using a tool known as a phaco-handpiece. The phaco-handpiece consists of a transducer that vibrates a needle that breaks up the lens in the eye. This broken lens is then aspirated through a tube through the centre of the transducer while water is continually supplied to the eye. Since the aspirated lens passes through the tool, it has to be sterilized after every use. This high-intensity energy sterilisation damages the electronics inside the handpiece, causing the lifespan of the handpiece to be shortened to only 200 uses when they could theoretically last over 1000 uses. Sterilisation also limits access to cataract surgery for hospitals that may not have access to large quantity, high-energy sterilisation.
Our goal was for a triple bottom line sustainable redesign of a phaco-handpiece. The new design aims to increase the lifespan of the rare piezo electronics, reducing e-waste (environmental), lower the upfront purchasing cost (economic), and increase access to the handpiece (social). We did this by creating a partially reusable and partially disposable handpiece.

Dutch Ophthalmic Research Center (DORC)
Project Client
DORC is an international supplier of instruments and equipment for ophthalmic surgery. They produce tools for anterior and posterior surgery and were looking for an innovative and sustainable alternative to cataract surgery.
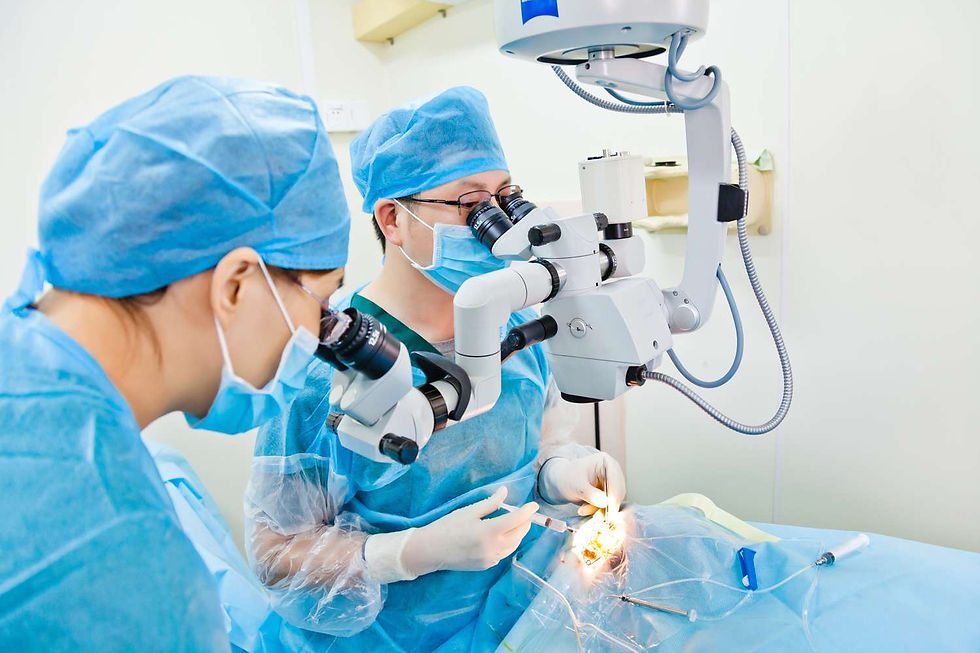
Introduction and Context
Cataract Surgery and Current Issues
Cataract surgeries are the most performed intervention in the world with over 28 million surgeries performed around the world each year. This means globally, there are nearly 60,000 cataract procedures every day .
There are a few techniques to perform this surgery, but the most common is phacoemulsification. Here, the opaque eye lens is emulsified and aspirated using a ‘phaco-handpiece’ and a new lens is then inserted using a secondary tool. The goal of this project is to redesign the DORC phaco-handpiece. The current product consists of a disposable needle and needle sleeve, as well as a reusable handpiece. The handpiece, however, undergoes an extensive sterilization process which reduces its life cycle and makes it less accessible to hospitals without the infrastructure to sterilize. We intend to develop a partially reusable and partially disposable handpiece to increase sustainability and access by increasing modularity and avoiding sterilization of the electronics. We want to ensure the best product experience for all parties involved while introducing these changes into our product.
Hospital environment
The tool is used in a sterile hospital environment where sterility, safety, and efficiency are given utmost importance.
The operating room is divided into two areas: sterile and non sterile. The sterile area is around the prepared patient where the doctor and scrub nurse are present along with the tools required for surgery. The doctor and scrub nurse are both covered in gloves, a gown, cap and a mask to ensure that there is no contamination. Additionally, sterile covers are draped around the patient and any equipment in the room such as the EVA Nexus. In the non sterile area there is a circulating nurse present to uncover any packaging for the sterile nurse to ensure that there is no contamination.
On average, 10 to 15 operations are performed per day (in the Netherlands) and the whole procedure from preparation to discharge of the patient takes about 20 to 25 minutes.
After each surgery, the handpieces are placed in a special container and then sterilised in-house or by external specialised bodies. This means that every hospital needs to have several sterile handpieces.
An important role during the entire surgical procedure is played by the nurses. They are responsible both for preparing the operating room with everything necessary and for providing the surgeon with the equipment to perform the operation.
Current Phacohandpiece
The Tool and its Working
The handpiece works using ultrasonic vibrations which are transferred to the needle through the acoustic horn. The needle breaks up the cataract and aspires the broken pieces. These pieces are sucked out through the aspiration tube. The irrigation tube supplies water to the eye through the sleeve to maintain pressure in the eye and ensure it does not overheat.
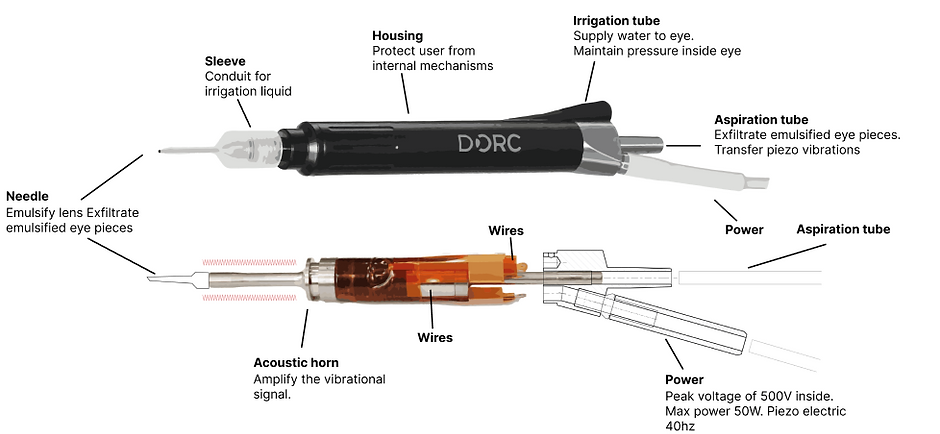
Where does the problem lie?
Since the aspirated lens passes through the tool, it has to be sterilized after every use. This high-intensity energy sterilisation damages the electronics inside the handpiece, causing the lifespan of the handpiece to be shortened to only 200 uses when they could theoretically last over 1000 uses. Sterilisation also limits access to cataract surgery for hospitals that may not have access to large quantity, high-energy sterilisation.
Design Vision and Requirements
“Design a modular and non-resource intensive handpiece that improves usability and allows for partial reusability.”


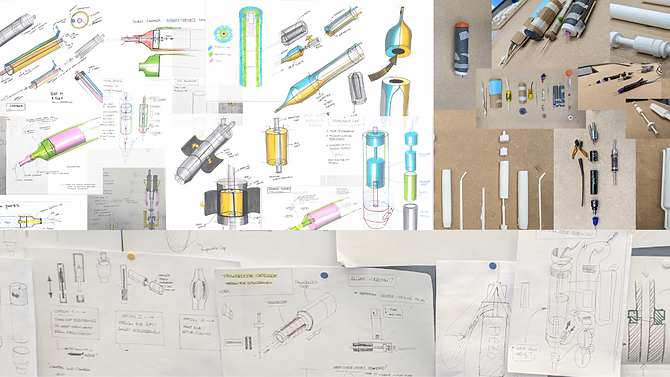
Iterative Ideation
After rounds of iterative ideation, low-fi prototyping and discussions with the clients, a rough concept was decided

Concept Freeze
Challenges with Manufacturing
The concept introduced a reusable transducer in a disposable housing to eliminate the need for sterilisation. However, this concept used a new design for the transmission shaft. This design could not be manufactured. Hence, the transmission shaft was redesigned and changed from a solid metal piece to two pieces: a flexible aspiration sleeve and a cylindrical transmission shaft.
Final Concept

The ultrasound is generated by piezo elements on the sonotrode that are translated to the transmission shaft to reach the needle.

The key change that allows the transducer module to be reused without becoming contaminated by biohazardous material is the rerouting of the aspiration tube. Instead of through the center of the handpiece, we divert it to the side before it reaches the electronics. The fluids are then aspirated by the needle, entering a new piece called the transmission shaft, then another new piece called the aspiration sleeve (blue).
Old versus New

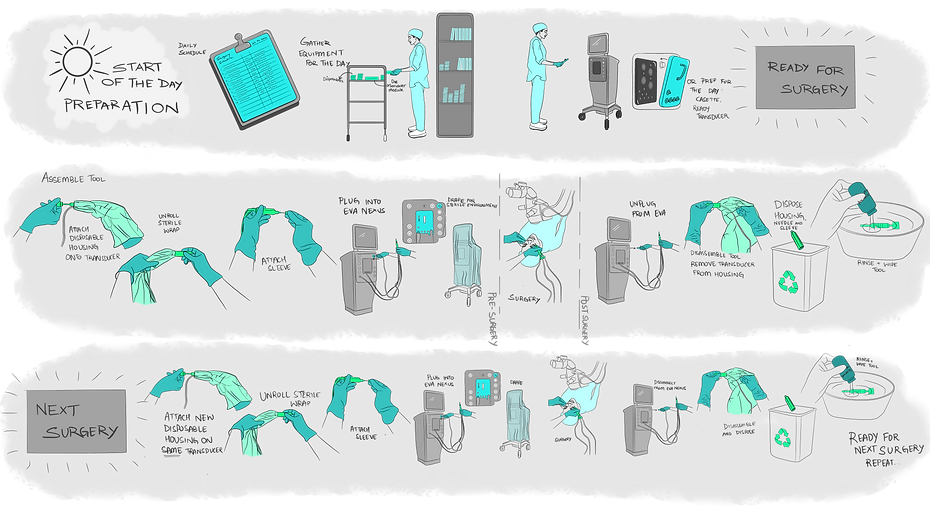
Bringing the vision to life

Reroute
Protect
Assemble

Reroutes aspiration fluid to the side of the handpiece

Protects transducer with a water-tight casing

Pre-assembled housing redesigned for ergonomics and reduction in assembly time

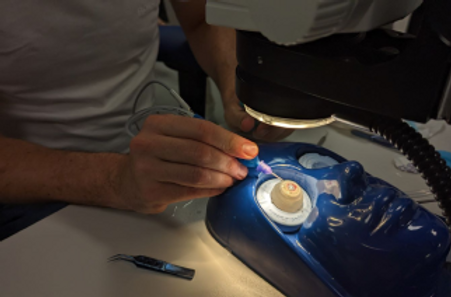
Testing
We were finally able to test this products in the hands of surgeons to perform cataract surgery on an artificial eye. The prototype was functional and aspirated the hard lens while providing irrigation. A single point of pride for me would be that the surgeons almost did not know that the technology was something we developed. They assumed it was part of DORC’s system showing us how seamless it felt to them. Additionally, they thought the redesigned shape was much more ergonomic and the length was a big improvement.
“So, the whole idea is great to have such a system, especially in some countries where sterilization is an issue”
- Ophthalmic surgeon